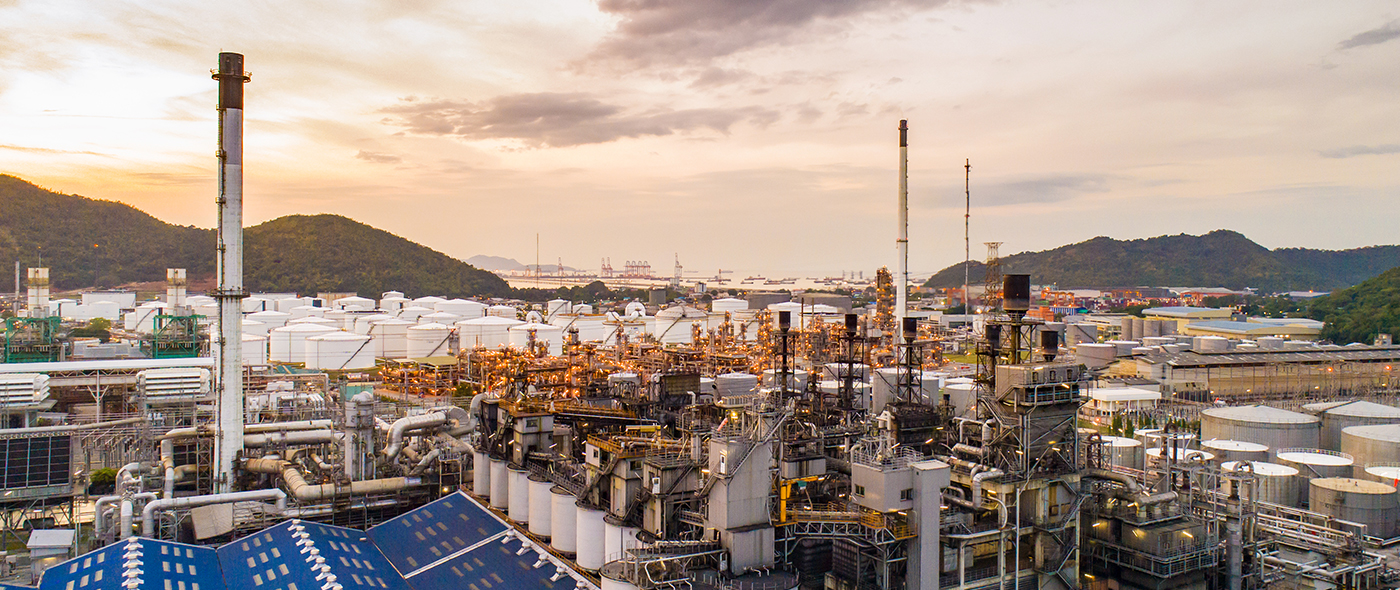
each with specific qualities such as strong reinforcement, high tensile strength and abrasive resistance, low shrinkage and high elasticity. Technological improvements in plant process have also allowed us to develop low grit carbon G-N550, G-N660 and G-N774 for very smooth surface products.
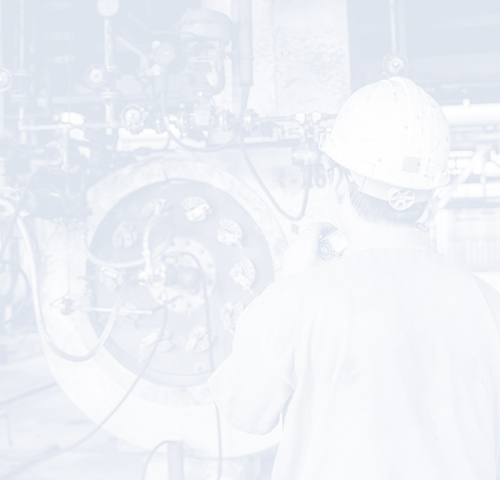
Feedstock oil, or a hydrocarbon compound from oil refining, is fed into an oil preheater and heated at 200 degrees Celsius to reduce its viscosity. Then, it is injected into the reactor and thermally decomposed at temperatures of 1300-1800 degrees Celsius in order to yield carbon black powder and tail gas.
The carbon black and tail gas mixture are then cooled to a temperature of 250-300 degrees Celsius. The carbon black is separated and filtered through a main bag filter while the tail gas is recycled for use in other process sections, which enables energy and production cost savings. It is then pulverized and formed into pellets for higher density to facilitate product handling. This process is monitored by closed circuit TV to ensure the right size of the carbon black pellets. Next, the pellets are dried in a rotary dryer where recycled tail gas is used as the source of heat. The dried carbon black pellets are moved to a vacuum-sealed conveyor belt system. A vibrating screen is used to regulate pellet sizes, while a rotary magnetic separator removes any impurities before loading into storage tanks. Quality testing is conducted both before and after storage to ensure the right quality of products.